DPM (Direct Part Mark) is a special mark making technology, not a bar code standard, generally called "direct part identification." This technology can be used to mark directly on the surface of components without the need for identification carriers such as paper and labels.
In the marking application of QR code, at present, our factory mainly adopts the method of automatic marking. After the workpiece is positioned and clamped, the proximity sensor sends the sensing signal to the PLC controller. According to the control logic, the controller sends the component identification code, the part number, the blank supplier code and the part number to the RS232 data line according to a certain format. The marking machine controller, after receiving the instruction of the PLC, the marking machine prints the above information on the workpiece in a two-dimensional code format. The scanner then scans the QR code. As shown in Fig. 1, pneumatic marking is used at the upper line of the cylinder line and the cylinder head line, and laser marking is used at the discharge port of the final inspection equipment of the crank line.
Figure 1 Two-dimensional code practical application
Two-dimensional code marking and scanning station introduction
Taking the cylinder head line as an example, the upper line marking scanning station of the two-dimensional code is set in the OP10, the lower line scanning station of the two-dimensional code is set in the quality gate (OP150), and the OP50 is the middle two-dimensional code scanning station. A lower-line scanning station similar to a two-dimensional code.
1. Two-dimensional code on-line marking scanning station
See Table 1 for the main equipment of the on-line marking scanning station.
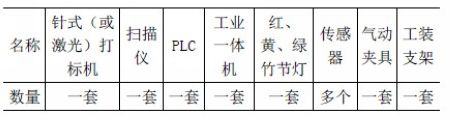
1) Click the “Cycle Start†button on the main interface of the HMI, the system starts running and the stopper is extended.
2) When the sensor senses the workpiece, the spacer mechanism acts to separate the second workpiece.
3) The clamping mechanism is extended to position and clamp the workpiece.
4) The judgment mechanism is extended to detect whether the supplier model of the workpiece is the same as the model set on the Panel (control board). If they are inconsistent, the system panel will alarm, the alarm light will alarm, and the system will stop running and wait for manual intervention.
5) The mobile mechanism moves the marking machine in place.
6) The system sends the marking serial number to the marking machine controller, and starts the marking machine to print the two-dimensional code.
7) The printing is completed, the marking machine is returned to the initial position, and the scanner is moved into position.
8) The system scans the QR code on the workpiece.
9) If the scan decoding fails, the system panel alarms, the bamboo light is red, and the refresh button light is on; the operator can press the rescan button to retry the scan and decode; or the operator can manually read the image by observing the image on the Panel. code.
10) If the scan is successful, but the content is the same as the last time, the system panel alarms, the bamboo light is red, and the refresh button light is on; the operator can operate according to the actual situation.
11) If the scan decoding is successful, the bamboo light will flash green and the fixture will loose open the workpiece.
2. Introduction to the offline scanning station of QR code
The main equipment of the offline scanning station is shown in Table 2.
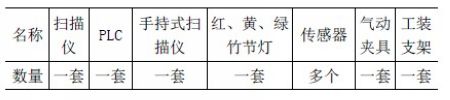
1) When the workpiece flows with the raceway to the lower line scanning station, the sensor detects the workpiece.
2) The scanner automatically scans, that is, photographs and decodes, and transmits the decoded information to the PLC.
3) If the scan decoding is successful, the bamboo light will flash green and the fixture will loosely open the workpiece.
4) The operator can monitor the scan result of the 2D scanner through the man-machine monitoring interface installed on the Panel.
5) If the scanner scan decoding fails, the system bamboo lamp automatically alarms, and the operator can manually input the two-dimensional code data in the input interface provided by the system according to the photo displayed on the panel, and the system automatically obtains the data as a scan. The information is passed to the PLC to complete the operation.
6) The system provides a hardware Rescan button for manually rescanning the QR code. When the automatic scan decoding fails, press this button to cause the scanner to rescan the QR code and try decoding again. If the button light is always on, it indicates that the function is valid.
7) The system provides a hardware ByPass (bypass function) button to force release of the currently operating workpiece. Press this button, the system releases the fixture and unconditionally discards the currently operating workpiece.
Information system query
To achieve the precise product traceability, product information inquiry and product measurement data queries are the two main means of product information via PT-MES, product measurement data query by Q-DAS in. The following is the specific query method.
1.PT-MES product information inquiry
For example, query the crankshaft product information: After logging in to the PT-MES system, visit the menu of "Production Control > Product Information Query > Product Information Query". You can select "product", "time", etc. as filtering criteria to narrow the scope of the query.
Column name explanation: 1) Serial number - the QR code on the workpiece. 2) Steel stamp number - the five-digit group number of the crankshaft . 3) Status - Product status (A indicates normal status, P indicates retirement status, and H indicates locked status). 4) Work station - the station that the workpiece has recently passed. 5) Operation code——Operation instruction executed by station: OP170 means automatic scanning of two-dimensional code; OP170M means manual input of two-dimensional code; QGH means manual locking of quality door; QGR means manual release of quality door; CPM means manual feeding waste state ; SCPW indicates manual labor waste status. 6) Number of quality gates—Quality gates that are not currently closed. The crankshaft line defines the OP170 as a manual visual inspection quality gate. After the workpiece is put on the line (OP160), the number of quality gates is 1. After the workpiece is manually visually inspected (OP170), the number of quality gates is zero.
2. Q-DAS measurement data query
OP50 JWF head to check leakage measurements, for example, operate on a Q-DAS software as follows: After opening the Q-DAS software, whether the database to confirm the machining line connection; Select "read from the database" data, Cylinder cover OP50 JWF measured value part name is 10020763, Cylinder Hea (JWF); pop-up confirmation window, select "Yes"; select "Value column" to display the measured value in the form of a list; right "Show attachment information field" to display traceability accessories code, the measurement date and time; the final display style.
Common problems and solutions for QR code traceability system
1. Two-dimensional code scanning rate is low
In the project acceptance phase, the problem of low pass rate of QR code scanning is often encountered. The following measures have been taken through analysis:
1) Increase the auxiliary light source to reduce background interference.
2) Using the anti-display principle, tilt the camera to increase the contrast of the light.
3) Adjust the focal length of the camera.
4) Deepen the print depth.
5) Change the needle regularly.
Through the implementation of the appeal measures, the current pass rate of QR code scanning reached 99.9%, which achieved the expected goal.
2. Consistency of scanning results
We have encountered such a situation: the workpiece scanned successfully on the crankshaft production line, the two-dimensional code scanner of the assembly line can not read the two-dimensional code of the crankshaft , causing confusion in the production organization. Later, the setting parameters of the two scanning guns of the crankshaft line and the assembly line were adjusted to make the reading ability and the reading effect completely identical, which solved the problem.
3. Disposal of waste and waste
Andon's count should be reduced after the scrap is processed, but in fact the count on Andon is cumulative. We require the supplier to modify the scan code of the manual scanner, and through the background processing of the PT-MES, ensure that the count on Andon is automatically reduced when scanning the scrap.
Conclusion
The two-dimensional code technology has its unique advantages in the manufacturing process of the engine and is the future development trend. However, the QR code traceability system is a systematic project involving the integration of operational processes, equipment adjustment, data uploading, system integration (PTMES, Q-DAS) and information management. Only the coordination of the above work is strict. According to the process, we can give full play to the advantages of this technology, making it an effective tool for quality traceability and production management.
Flanged Stainless Steel Ball Valve
Flanged Stainless Steel Ball Valve,Ss Ball Valve,Stainless Ball Valve,316 Stainless Steel Ball Valve
Zhejiang Chenxiang import and export trade Co., Ltd , https://www.chenxiang-valve.com