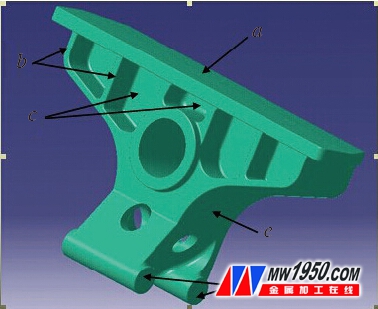
Figure 1 bracket 3D solid
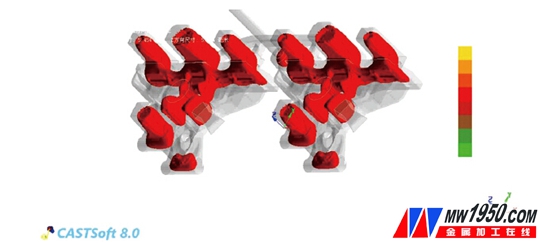
Figure 2 Cooling time t = 180.68s The solidification process is 52.44%
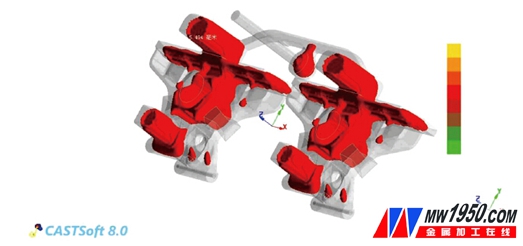
Figure 3 Cooling time t = 154.94s The solidification process is 45.06%
About the author: Zhang Fubin, Gao Xiuwu, Dai Fangzheng, Wang Chengliang, China National Heavy Duty Truck (Hong Kong) Co., Ltd. Jinan Casting and Forging Center.
A Towel bar is an easy way to keep your bathroom looking tidy, while helping your towels dry more quickly. Different towel bars can accommodate more towels, whether you're looking for a single or double towel bar. And most towel bars are wall-mounted. You can buy your bathroom towel bar in a range of finishes to match other bathroom accessories, such as chrome towel bars, brushed nickel towel bars, gold towel bars, or even modern matte black towel bars.
Towel Bar,Towel Bar Supporing Chrome,Washroom Towel Bar,Height of Towel Bar
Kaiping Jenor Sanitary Ware Co., Ltd , https://www.jenorsanitary.com