ã€China Aluminum Network】 Aluminum extrusion refers to the aluminum alloy high temperature casting billet into a special mold, under the pressure of the extruder to provide a strong force, according to the given speed, the aluminum alloy extrusion from the cavity , In order to obtain the desired shape, size and aluminum alloy extruded profiles with certain mechanical properties. Aluminum extrusion molding process is very complicated, in addition to the extrusion of circular and circular section aluminum profile is a two-dimensional axisymmetric problem, in general, other shapes of aluminum extrusion is a large three-dimensional flow deformation problem. Therefore, the quality of the extrusion die design and its service life become one of the keys to the economic feasibility of the extrusion process. Reasonable design and manufacturing can greatly extend the life of the mold, which is of great significance for improving the production efficiency, reducing the cost and energy consumption. At present, China's profile extrusion die design basically remains in the traditional accumulation of engineering analogy and design experience. In fact, the more complex the profile section, the more pronounced the non-uniformity of the extrusion deformation, resulting in the new design of the mold is difficult to guarantee a uniform outflow of the billet, causing the profile due to twisting, waves, bending and cracks Defective and scrapped, the mold is also very easy to damage, must go through repeated trial mode, repair mode can be put into normal use, resulting in waste of funds, manpower, time, resources, etc. [1]. Therefore, with the continuous development of aluminum profile products to large-scale, flattened, thin-walled, highly refined, complicated and multi-purpose, multi-functional, multi-variety, long-life, improving the traditional mold design method has become the current The urgent needs of aluminum industry development.
1 Significance of Aluminum Profile Extrusion Die CAE Technology Aluminum Profile Extrusion Die CAE technology is a numerical value that uses the extruded product model established in CAD, combines extrusion process and control parameters, completes the analysis of its forming process, and optimizes the corresponding mold design. technology.
The specific approach is: based on the preliminary design of the extrusion die, according to a preliminarily prepared process test plan, using the computer to simulate the entire extrusion process, physical stress distributions such as stress, strain, temperature, and flow velocity in the extrusion body are obtained and squeezed. Pressure process conditions such as pressure, temperature, and speed are determined at each stage. The influence of mold sections such as the cross-section of the extrusion die and the diverter holes, weld cavities, diversion grooves, etc. on the flow of the formed aluminum is determined. The mold may appear during use. Deformation, collapse, chipping, cracking, wear, "sticking" and fatigue and other defects and their location; put forward analysis report and recommend suitable extrusion conditions to the designer, the designer then corrects the die design program according to CAE analysis results. After several iterations, until the mold design program meets product design requirements and product quality requirements [2]. This is actually the process of transferring the “trial-modification-testing†process at the production site to the computer to partially replace the time-consuming and costly test-work in the mold design and manufacturing process, thereby reducing the material and energy consumption at this stage. Reduce production costs and design high-quality aluminum extrusion dies.
Although CAE technology has obtained some successful applications in the field of aluminum extrusion die design and manufacturing, it is rarely applied to mold engineers. This is mainly due to the fact that CAE software has not been specifically developed for extrusion molding of aluminum profiles at home and abroad. Therefore, when mold engineers use some common or special CAE software (such as ANSYS/LSDYNA, MARC/AutoForge, Deform, etc.) to carry out mold design When analyzing the mold structure, in addition to requiring the user to have a solid extrusion process and extrusion mold design manufacturing expertise, and to be familiar with the working conditions of the extrusion mold components in the coupled field environment, he is also required to conduct numerical simulation techniques and The corresponding finite element analysis method must have a deeper understanding, which is more difficult for engineering and technical personnel working in the front line of production. This is one of the important reasons why CAE technology is not widely used in the extrusion die industry. .
The application of aluminum extrusion die CAE can shorten the design and manufacturing cycle of the die, improve the quality of the die, and enhance the market competitiveness of the enterprise. However, only by solving the above problems can CAE technology be widely used in the extrusion die industry. This is the significance of the aluminum extrusion die CAE technology research.
The current situation of optimization design of aluminum extrusion die Because it is a very complicated and difficult job to design a extrusion die with reasonable structure and economical practicality, therefore, extrusion workers in all countries in the world have theories and methods for die design (especially The optimization theory and method) carried out a lot of research work.
At the beginning of the development of extrusion technology, mold design was generally based on mechanical design principles using traditional strength theory combined with the designer's practical experience. With the development of elasto-plastic theory and extrusion theory, many new experimental theories and methods, computational theories and methods have begun to be used in the field of extrusion die design and fabrication. For example, engineering calculation method, metal flow coordinate grid method, photoelastic light-plastic method, dense grid pattern method, slip line method, upper limit element theory, and finite element theory are widely used in the determination of mold strain field and various The strength of the check, and then optimize the structure and process elements. With the development of computer technology, the CAD/CAM technology of extrusion die has been rapidly developed in the near 2030, and a large part of the technology is focused on the optimization of die design. He Delin et al.[3] developed a CAD/CAM system that can optimize the planar die and the splitter die using the IDEF0 method; Wang Mengjun et al.[4] used AUTOCAD120 as the graphics support environment and VISUAL BASIC4.0 as the development tool to develop the CAD. The system can effectively perform various calculations of the extrusion die, thus optimizing the design results; Yan Hong et al. [5] introduced the CAE concept into the die design process and pointed out the direction of optimization design; Liu Hanwu et al. [6] The concept of intelligent CAD was proposed to provide some ideas for the intelligent design of molds. In addition, researchers at home and abroad have used theoretical analysis, physical simulation and numerical simulation to analyze and test the deformation process, distribution and change of stress field and temperature field, friction and lubrication of aluminum extrusions. According to its research results, the extrusion die was optimized. For example, Zhao Yunlu and Liu Jingan [7] systematically discussed the optimization design of various extrusion dies. Some domestic researchers have used the finite element method combined with experimental methods to analyze and optimize the profile and mold structure of the extrusion die.
However, due to the thinness of mold technology, China started late, and there is still a certain gap compared with foreign counterparts at the comprehensive level.
1 2
Deep Groove Ball Bearings
Deep groove ball bearings The out looks of them are nearly the same,the only different is the size,you may need other models please check the following table for reference.are the most widely used bearing type and are particularly versatile.
They have low friction and are optimized for low noise and low vibration which enables high rotational speeds.
They accommodate radial and axial loads in both directions, are easy to mount, and require less maintenance than other bearing types.
Deep groove ball bearings are divided into the following series: 6000series, 6100series, 6200series, 6300series, 6400 series, 6700 series, 6800 series,6900 series,16000 series etc.
Model |
d(mm) | D(mm) | B(mm) |
6000ZZ |
10 | 26 | 8 |
6001ZZ | 12 | 28 | 8 |
6002ZZ | 15 | 32 | 9 |
6003ZZ | 17 | 35 | 10 |
6004ZZ | 20 | 42 | 12 |
6005ZZ | 25 | 47 | 12 |
6006ZZ | 30 | 55 | 13 |
6007ZZ | 35 | 62 | 14 |
6008ZZ | 40 | 68 | 15 |
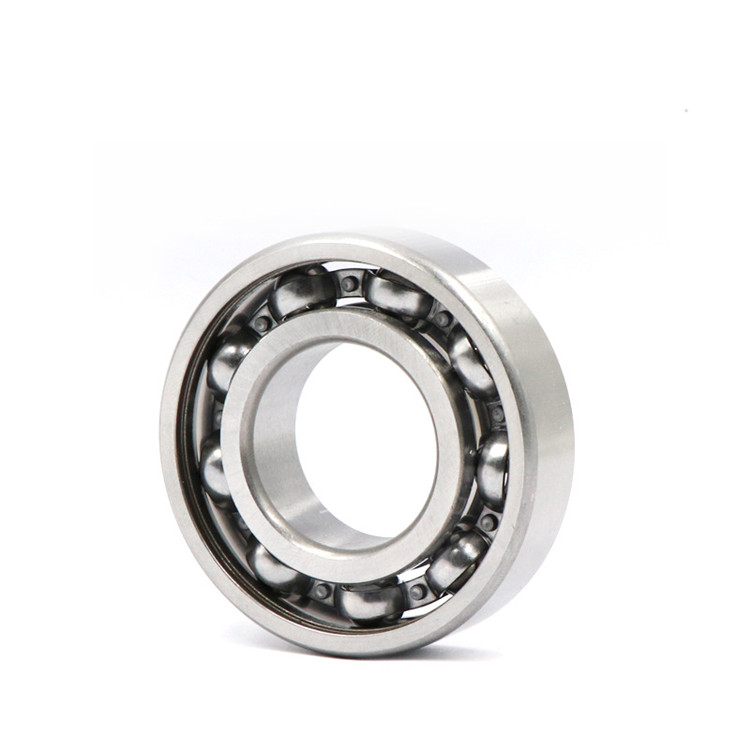
We manage in all kinds of ball bearings and roller bearings,such as
1.Deep Groove Ball Bearing
2.Self-aligning Ball Bearing
3.Cylindrical Roller Bearing
4.Spherical Contact Bearing
5.Angular Contact Bearing
6.Tapered Roller Bearing
7.Thrust Ball Bearing
8.Insert Bearing
Package
1.Small bearings|:plastic tube+carton+pallet
2.Medium bearings:PE bag+box+carton+pallet
3.Large bearings:PE film & paper winding+carton+pallet
4.According to the customer's requirements
High Ball Bearing,Miniature Ball Bearing,Deep Groove Ball Bearing,Deep Ball Bearing
Shijiazhuang Longshu Mechanical & Electrical Equipment Trading Co., Ltd. , https://www.longsbearing.com